Ever looked at a tin can and wondered how it’s made? It’s something we use daily, yet most of us have no clue about the complex process behind it. Let’s unravel the tin can production process with tin cans manufacturer, step by step, and see how simple sheets of metal transform into the trusty containers that keep our food fresh and safe.
What Is a Tin Can?
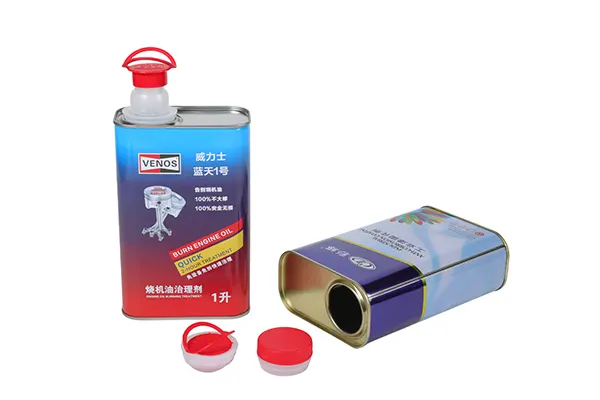
A tin can is a container made primarily from tin-coated steel. This combination of metals creates a durable, corrosion-resistant vessel ideal for storing food, 음료수, 페인트, engine oil and other goods. The tin layer acts as a protective barrier, preventing the steel from rusting and ensuring the contents remain uncontaminated. Tin cans are ubiquitous in modern packaging, thanks to their strength, light weight, and ability to preserve freshness.
단계 #1: Preparation of Raw Materials
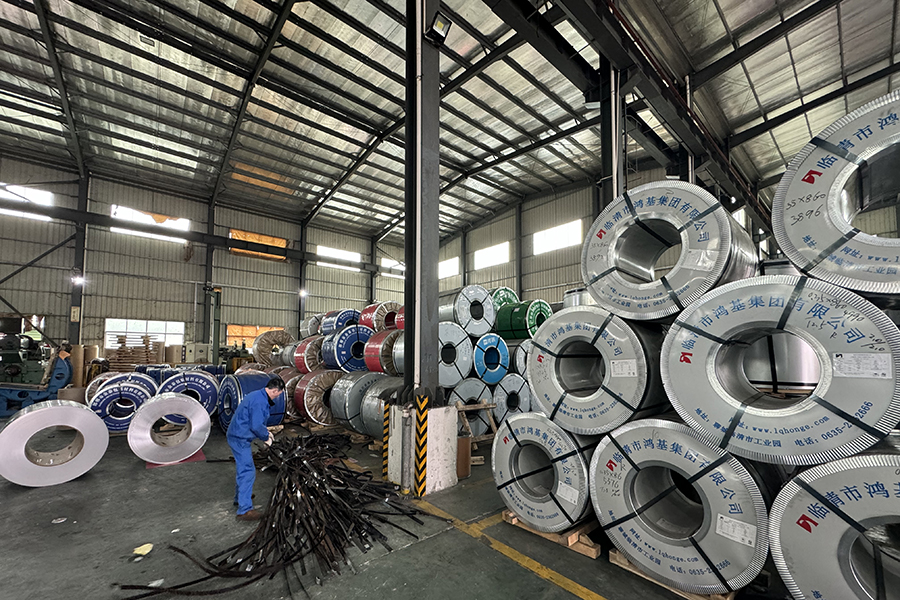
Mining and Processing Tin
The journey of a tin can begins in the earth. Tin is mined from the ground in the form of cassiterite ore. This ore is then processed and refined to extract pure tin. This pure tin is essential because it’s corrosion-resistant, making it perfect for food storage.
Producing Steel Sheets
강철, the backbone of our tin can, is produced in large sheets. Iron ore is smelted in blast furnaces to produce molten iron, which is then mixed with carbon to create steel. These steel sheets provide the strength and durability that tin cans need to withstand handling and storage.
단계 #2: Cutting and Shaping
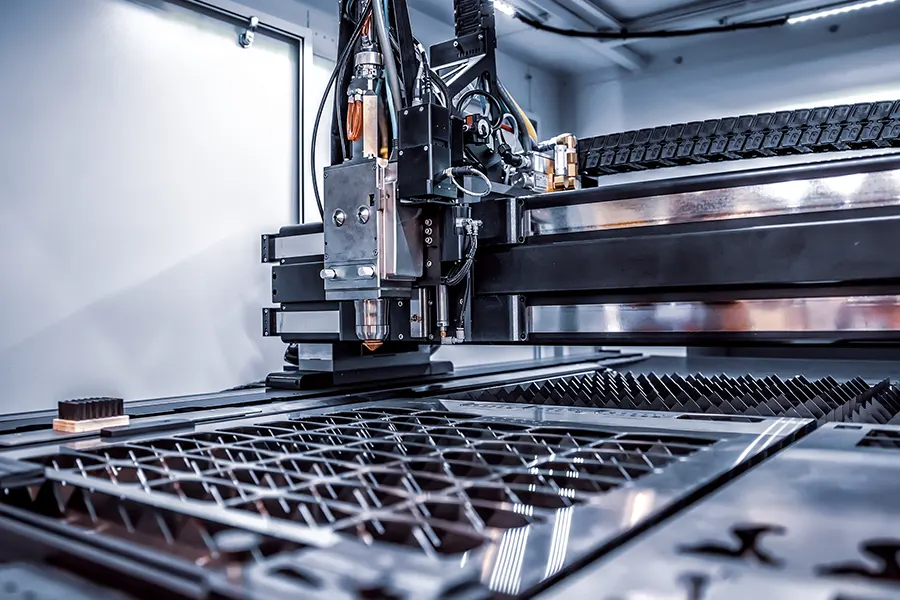
Sheet Cutting
Once we have our raw materials, the next step in the tin cans manufacturing process is cutting the steel sheets into smaller, manageable pieces. Imagine slicing a giant cookie dough into smaller shapes – that’s what happens with the steel sheets.
Forming the Can Body
These cut pieces are then shaped into cylindrical forms. Picture rolling a piece of paper into a tube; that’s essentially what happens here. This cylinder will become the body of our tin can. It’s then ready to move on to the next stage.
단계 #3: Welding and Seaming
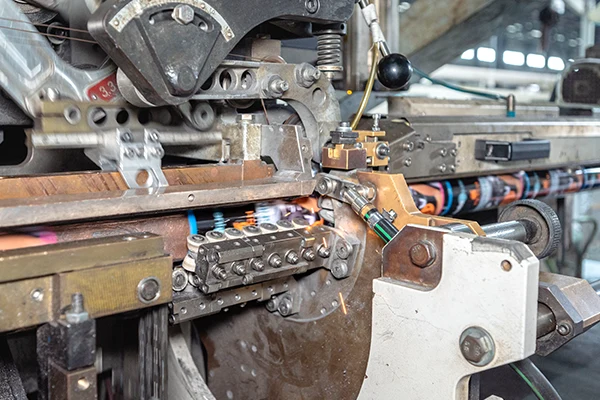
Body Welding
The edges of the cylindrical steel pieces are welded together. This welding process ensures the body of the can is airtight and secure. Think of it as zipping up a jacket – it keeps everything snug and in place.
Attaching the Bottom and Top
다음, the bottom and top of the can are attached. This is done through a process called seaming, where the edges are folded and compressed to form a tight seal. It’s like putting a lid on a jar, but much more permanent and secure.
단계 #4: Coating and Lining
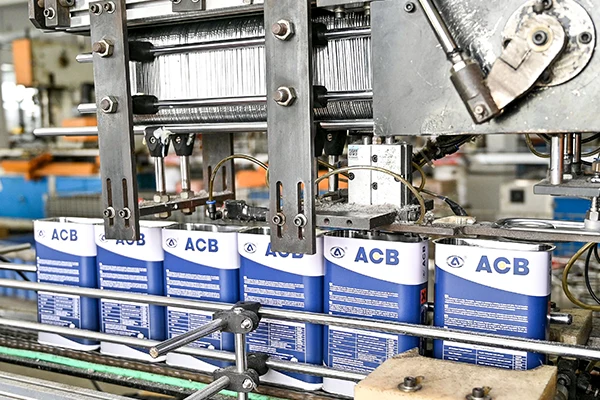
Internal Coating
To protect the contents of the can from reacting with the metal, an internal coating is applied. This coating acts like a protective shield, ensuring the food stays fresh and untainted.
External Painting
The outside of the can is painted to prevent rust and give it a finished look. This step also involves adding labels and branding, transforming a plain metal cylinder into a recognizable product on store shelves.
단계 #5: 품질 관리
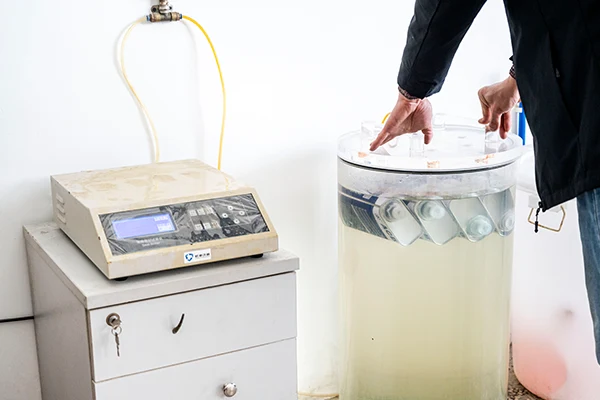
Before tin cans hit the market, they undergo rigorous quality control checks. Automated systems inspect each can for defects, and manual inspections are conducted to catch anything the machines might miss. This ensures that only the best cans make it to your pantry.
결론
And there you have it – the intricate journey of how tin cans are made. From raw materials to the final product, each step in the tin container manufacturing process is meticulously planned and executed to ensure we get reliable, durable cans that keep our food safe. So, the next time you open a can of soup or beans, you’ll know the incredible journey it has been through to get to your kitchen.
FAQs on Tin Cans
- What are tin cans made from? Tin cans are primarily made from tin and steel, with additional coatings for protection.
- Why is an internal coating used in tin cans? The internal coating prevents the food from reacting with the metal, ensuring it remains fresh and safe.
- How are steel sheets prepared for can production? Steel sheets are cut into smaller pieces and then formed into cylindrical shapes to create the can body.
- What is seaming in the tin can production process? Seaming is the process of attaching the bottom and top of the can by folding and compressing the edges to form a tight seal.
- Why is quality control important in tin cans manufacturing? Quality control ensures that only defect-free cans reach consumers, maintaining the safety and integrity of the packaged food.